Understanding and Resolving Die Casting Defects
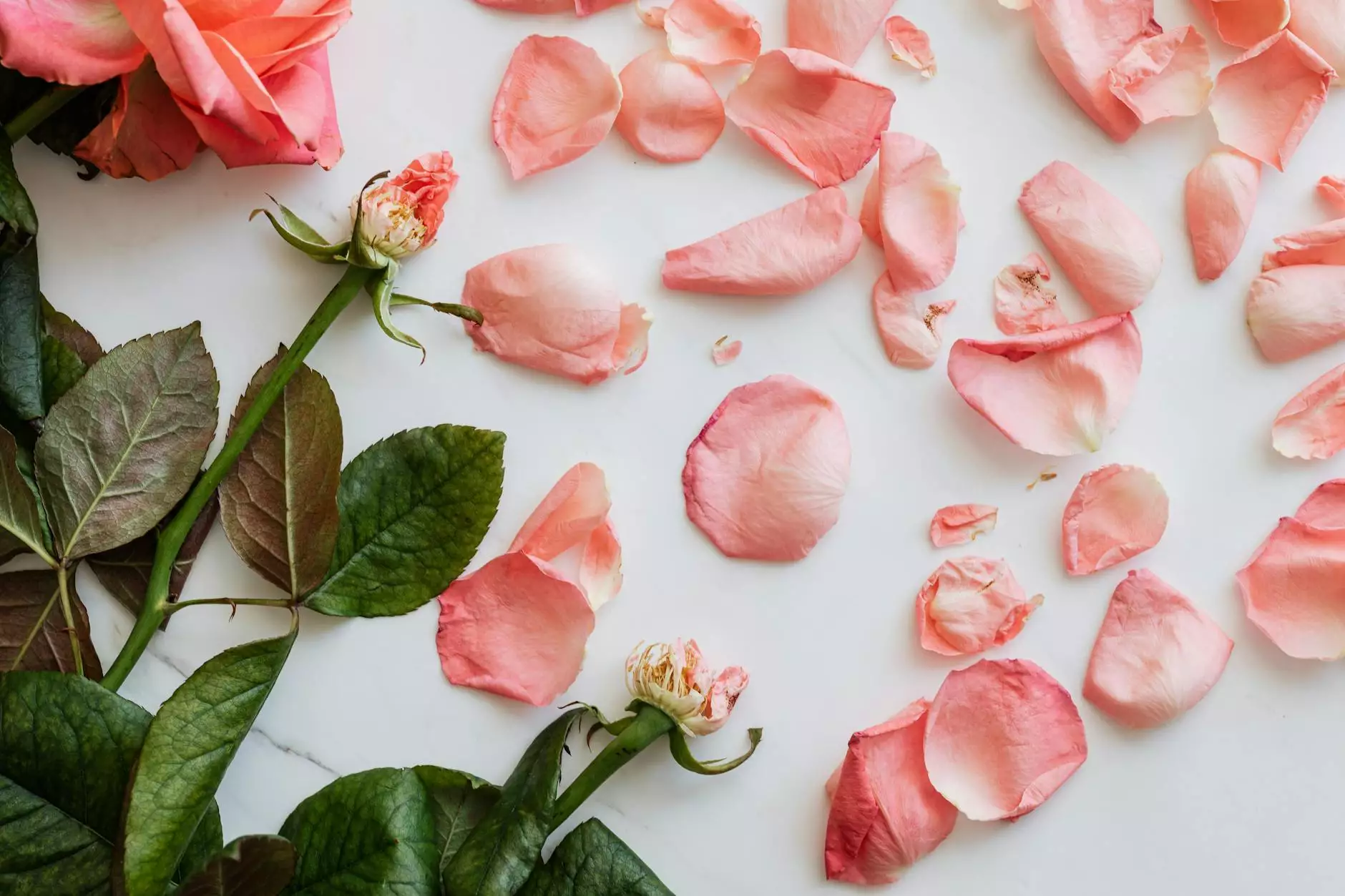
Welcome to Wetron Industrial, your trusted partner in providing top-notch die casting products for the Home & Garden and Appliances industries. In this article, we will delve into the world of die casting defects, exploring their causes and offering effective solutions to help you create flawless components for your business.
What are Die Casting Defects?
Die casting is a manufacturing process used to produce complex and high-quality metal parts or components. However, like any other manufacturing process, die casting is not without its share of challenges.
Die casting defects refer to imperfections or irregularities that may occur during the die casting process, resulting in components that do not meet the desired specifications. These defects can impact the functionality, reliability, and aesthetics of the final product.
Common Types of Die Casting Defects
1. Porosity
Porosity is one of the most prevalent die casting defects. It occurs when small air pockets or voids form within the casting material. These voids can weaken the component, compromising its structural integrity. Porosity is often the result of improper venting, inadequate die temperature control, or impurities in the alloy.
2. Shrinkage
Shrinkage defects are caused by the contraction of the metal during solidification. These defects usually occur when the metal cools too quickly or when there is not enough material in the die. Common signs of shrinkage include voids, sink marks, or dimensional inaccuracies.
3. Cold Shut
Cold shut defects occur when two flow fronts do not fuse properly during the casting process, resulting in a visible line or seam on the surface of the component. Cold shuts can weaken the structural integrity of the part and affect its appearance. Improper gating system design, low metal temperature, or excessive turbulence are common causes of cold shuts.
4. Flash
Flash defects refer to thin layers of excess material that are expelled from the casting and remain attached to the component after the casting process. Flash can be unsightly and may interfere with the functionality of the part. It is usually caused by excessive injection pressure, worn-out die components, or poorly maintained casting equipment.
5. Misruns
Misruns occur when the molten metal fails to completely fill the die cavity. This defect often results in incomplete or distorted parts. Misruns can be caused by insufficient injection pressure, inadequate gating design, or improper die temperature control.
Resolving Die Casting Defects
At Wetron Industrial, we understand the importance of delivering defect-free die cast components. Our expert team employs a range of techniques and best practices to minimize defects and optimize the quality of our products.
1. Advanced Mold Design
Proper mold design is crucial in preventing die casting defects. Our team utilizes state-of-the-art software to create precise and customized molds that ensure optimal fill and minimize the risk of defects. We analyze the flow of molten metal, identify potential problem areas, and make necessary adjustments to guarantee high-quality castings.
2. Optimal Process Parameters
Controlling the process parameters is key to achieving defect-free castings. We carefully monitor variables such as temperature, pressure, and injection velocity to ensure the molten metal fills the cavity uniformly and solidifies without any defects. Our experienced technicians fine-tune these parameters for each specific alloy, optimizing the casting process.
3. Thorough Quality Checks
Quality checks are an integral part of our production process. We employ non-destructive testing methods, such as X-ray and ultrasound inspections, to detect any hidden defects within the castings. Our commitment to stringent quality control measures ensures that only flawless components reach our customers.
4. Continuous Improvement
At Wetron Industrial, we believe in constantly striving for improvement. We regularly assess our manufacturing processes, analyze defect data, and implement corrective measures to enhance our casting techniques. This commitment to continuous improvement allows us to stay at the forefront of the industry, providing our customers with superior die cast products.
Conclusion
In summary, understanding and resolving die casting defects is crucial for producing high-quality components in the Home & Garden and Appliances industries. Wetron Industrial is dedicated to delivering flawless die castings, utilizing advanced mold design, optimal process parameters, thorough quality checks, and a commitment to continuous improvement. Partner with us to benefit from our expertise and uncompromising commitment to quality.