Die Casting Defects Explained
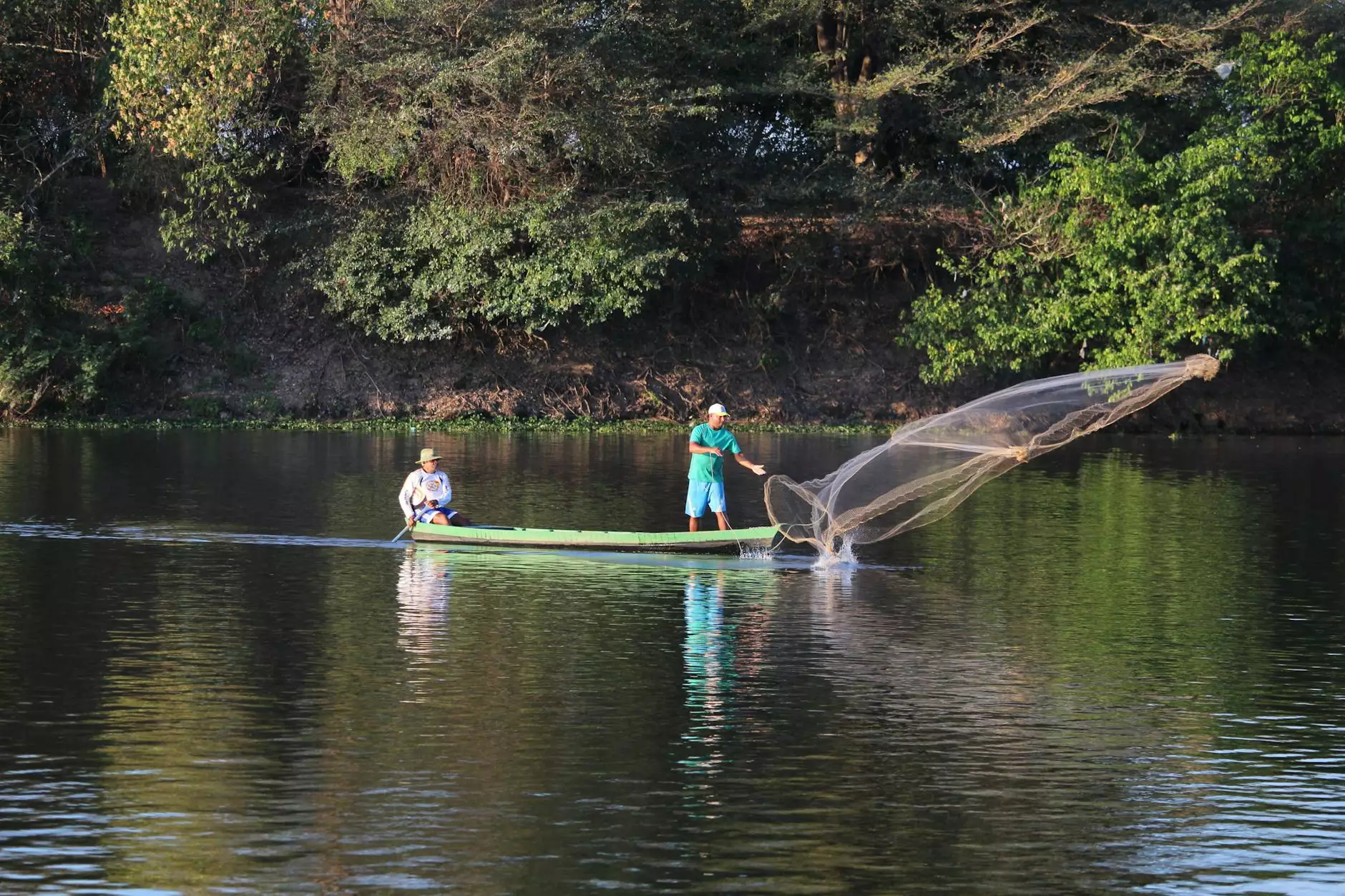
As an industry leader in the Home & Garden, Appliances sector, Wetron Industrial aims to provide its customers with the highest quality die casting products. Our expert team is dedicated to ensuring that each component produced meets the strictest standards and exceeds customer expectations.
The Importance of Die Casting in the Home & Garden, Appliances Industry
Die casting plays a crucial role in the manufacturing of many Home & Garden, Appliances products. It is a cost-effective method that allows for the production of intricate and durable parts with excellent dimensional accuracy. However, like any manufacturing process, die casting is not without its challenges, and one key area that requires attention is the prevention and elimination of die casting defects.
Understanding Die Casting Defects
Die casting defects are anomalies or imperfections that occur during the manufacturing process and can adversely affect the quality and functionality of the final product. Identifying and rectifying these defects is essential to ensure the integrity and reliability of the components produced.
Common Die Casting Defects
Wetron Industrial has identified and resolved several die casting defects that are prevalent in the Home & Garden, Appliances industry. By understanding these defects, manufacturers can take proactive measures to minimize their occurrence:
- 1. Porosity: Porosity refers to the presence of small voids or gas pockets in the metal casting. It can compromise the structural integrity and strength of the component. Measures such as adjusting the die temperature, using proper venting, and optimizing the alloy composition can help reduce porosity.
- 2. Shrinkage: Shrinkage occurs when there is inadequate material flow during the solidification phase, resulting in small cavities or voids. Proper gating and riser design, as well as optimizing cooling systems, can help minimize shrinkage defects.
- 3. Cold Shut: Cold shut defects occur when two or more streams of molten metal fail to fuse properly during the casting process. This can lead to weak joints and compromised component integrity. Effective gating, precise control of metal temperature, and optimizing the die design can help prevent cold shut defects.
- 4. Flash: Flash defects appear as thin, unwanted metal projections along the parting line of a die casting. They are caused by excessive molten metal seepage through the parting surfaces. Proper clamping forces and well-maintained dies can help prevent flash defects.
Overcoming Die Casting Defects with Wetron Industrial
At Wetron Industrial, we understand the significance of defect-free die castings in the Home & Garden, Appliances industry. We leverage our expertise and state-of-the-art equipment to minimize and eliminate die casting defects for our clients.
Our Approach:
1. Advanced Simulation: Before beginning the production process, our team utilizes advanced simulation software to identify potential defects and optimize the die design accordingly. This ensures a smoother manufacturing process and reduces the chances of defects.
2. Material Selection: We carefully select the appropriate alloys with the desired mechanical and physical properties, reducing the occurrence of defects during the casting process.
3. Precise Process Control: Wetron Industrial maintains stringent process control measures to ensure consistent product quality. Our experienced operators monitor critical parameters such as temperature, pressure, and cooling rates to minimize defects.
4. Robust Quality Control: We have a dedicated quality control team that conducts thorough inspections at each stage of the die casting process, from raw material inspection to post-casting finishing. This comprehensive approach guarantees defect-free components.
Conclusion
In the highly competitive Home & Garden, Appliances industry, manufacturers need to produce die castings with exceptional quality and precision. By partnering with Wetron Industrial, businesses can benefit from our extensive experience in mitigating die casting defects. Our commitment to excellence and cutting-edge manufacturing techniques ensure that our customers receive superior components that meet their exact specifications.
For reliable and defect-free die casting solutions, choose Wetron Industrial. Contact us today to discuss your project requirements and experience the difference firsthand.