Understanding Prototype Injection Molding: A Comprehensive Guide
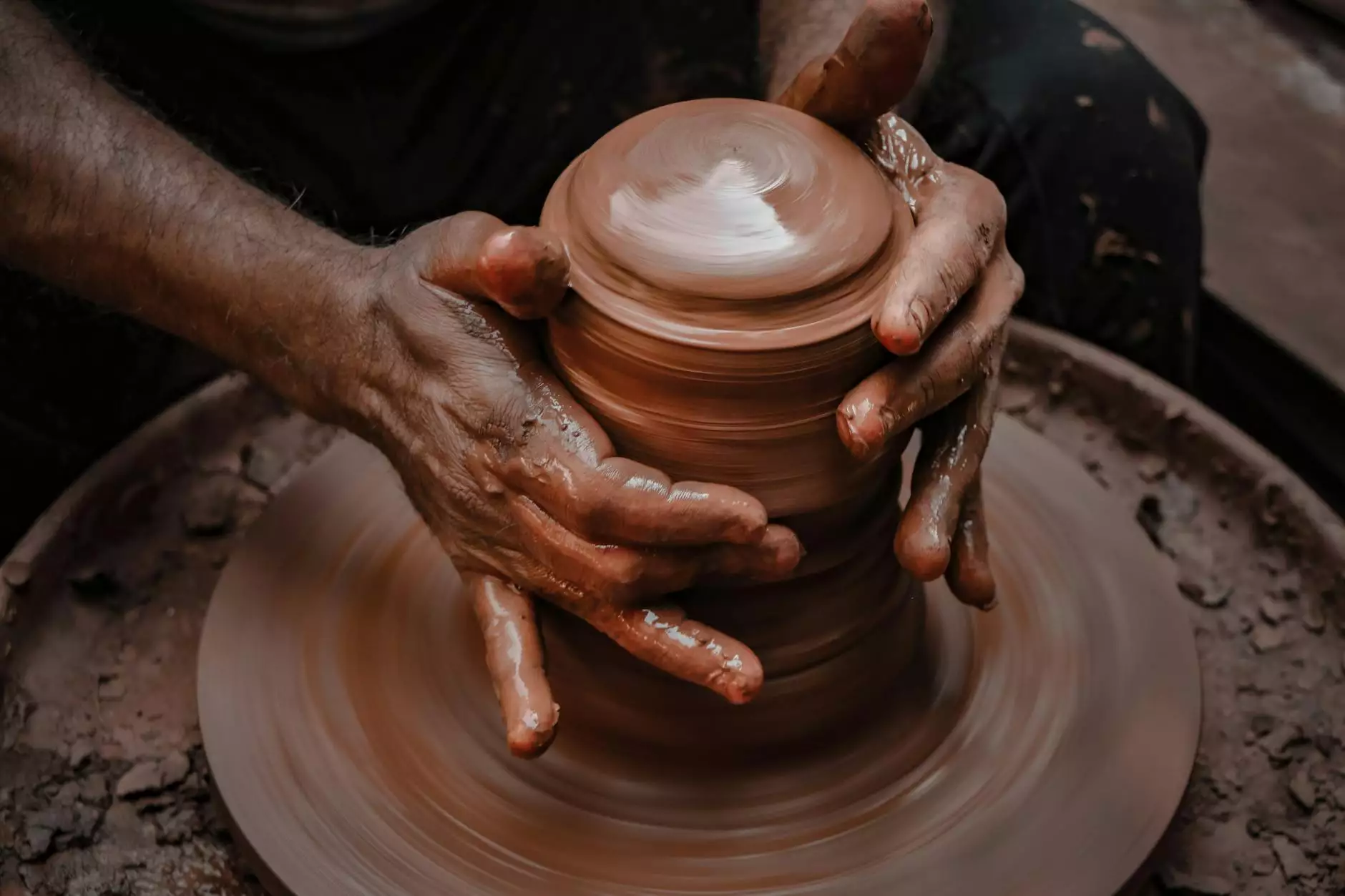
Prototype injection molding stands as a pivotal process in the realm of modern manufacturing, particularly within the category of metal fabricators. This technique not only allows for rapid development and iteration of product designs, but also reduces costs and time associated with traditional manufacturing methods. As industries increasingly turn towards innovative solutions, understanding this process becomes essential for anyone involved in product development.
What is Prototype Injection Molding?
Prototype injection molding is a manufacturing process used to create parts by injecting molten material—commonly thermoplastics—into a mold. This method allows for the quick and cost-effective production of parts and prototypes, enabling designers and engineers to bring their ideas to life efficiently.
How Does the Process Work?
The process of prototype injection molding involves several key stages:
- Material Selection: The first step is to select an appropriate material based on mechanical properties, thermal resistance, and the specific requirements of the end-use application.
- Mold Design: A detailed design for the mold is created, taking into account the final product's geometry and functionality. This stage often involves 3D modeling software.
- Mold Fabrication: Using CNC machining or other techniques, the mold is fabricated. This stage is crucial as even minor errors can lead to defective products.
- Injection Molding: The selected material is heated until it melts and is then injected into the mold under high pressure, filling the cavity.
- Cooling Time: The material is allowed to cool and solidify in the mold before it is ejected.
- Post-Processing: The product may undergo secondary operations like trimming, painting, or assembly.
Advantages of Prototype Injection Molding
The benefits of using prototype injection molding in product development are vast:
- Speed: The entire process, from design to prototype, can often be completed within weeks, drastically reducing the time to market.
- Cost-Effectiveness: Although mold fabrication can be costly, the ability to produce high volumes of parts at lower costs offsets this investment.
- High Precision: Injection molding produces parts with excellent dimensional accuracy and repeatability.
- Material Versatility: A wide range of materials can be used, including various metals and polymers, which can be tailored to specific application needs.
- Scalability: Transitioning from prototypes to large-scale production is seamless, allowing for a smooth process when moving to full-scale manufacturing.
Applications of Prototype Injection Molding in Metal Fabrication
In the metal fabricators category, prototype injection molding has a multitude of applications:
1. Automotive Industry
Prototype injection molding plays a critical role in the automotive sector, where components such as dashboards, casings, and even small engine parts are produced in high volumes. The ability to prototype quickly enables manufacturers to iterate designs and innovate faster.
2. Consumer Electronics
The consumer electronics industry leverages prototype injection molding to develop housings, connectors, and various components that require high precision and durability.
3. Medical Devices
In the medical field, the precision of prototype injection molding is crucial. Components for devices such as syringes, implants, and diagnostic equipment are routinely produced using this technique, with stringent compliance to regulatory standards.
4. Industrial Equipment
Components for machinery, tooling parts, and equipment housings can be effectively created using prototype injection molding, providing the strength and resilience required for industrial applications.
Challenges in Prototype Injection Molding
While there are numerous advantages, there are also challenges associated with the process:
- Initial Costs: The upfront cost for developing molds can be significant, particularly for complex designs.
- Long Lead Times: Depending on the complexity of the project, the design and fabrication of molds can take time, delaying the prototyping phase.
- Material Limitations: Not all materials are suitable for injection molding, and selecting the correct material is essential to meet performance criteria.
Best Practices for Successful Prototype Injection Molding
To maximize the benefits of prototype injection molding, manufacturers should consider the following best practices:
1. Collaborative Design
Engaging multiple stakeholders, including designers, engineers, and manufacturing specialists during the design phase leads to better outcomes and fewer revisions down the line.
2. Optimize Mold Design
Utilizing advanced modeling software to optimize mold design can lead to improved efficiency and lower operational costs during the injection molding process.
3. Material Testing
Conduct thorough material testing to ensure chosen materials meet the specific demands of the application, thereby avoiding costly mistakes.
4. Continuous Improvement
Establishing a feedback loop that allows for the evaluation of prototypes and processes can lead to continuous improvement and innovation in the product development cycle.
The Future of Prototype Injection Molding
As industries continue to embrace technological advancements, the future of prototype injection molding looks promising. Innovations such as:
- 3D Printing Integration: The combination of 3D printing technologies with traditional injection molding is paving the way for more intricate designs and quicker prototyping.
- Smart Manufacturing: The integration of IoT (Internet of Things) in manufacturing processes, including injection molding, will enhance efficiency and reduce wastage.
- Advanced Materials: Development in material science could present new opportunities for stronger, lighter, and more versatile materials suitable for injection molding.
Conclusion
In conclusion, prototype injection molding is a critical component of the manufacturing process in the metal fabrication sector. Its ability to streamline production, reduce costs, and enhance the design process makes it an invaluable tool for engineers and product developers alike. By understanding the intricacies of this process and adhering to best practices, businesses can leverage its full potential to innovate and remain competitive in an ever-evolving market.
For businesses looking to adopt this technology, partnering with experienced mold fabricators, such as those found on deepmould.net, can provide the expertise and resources necessary to succeed.