CNC Machining Part Factories: Revolutionizing Metal Fabrication
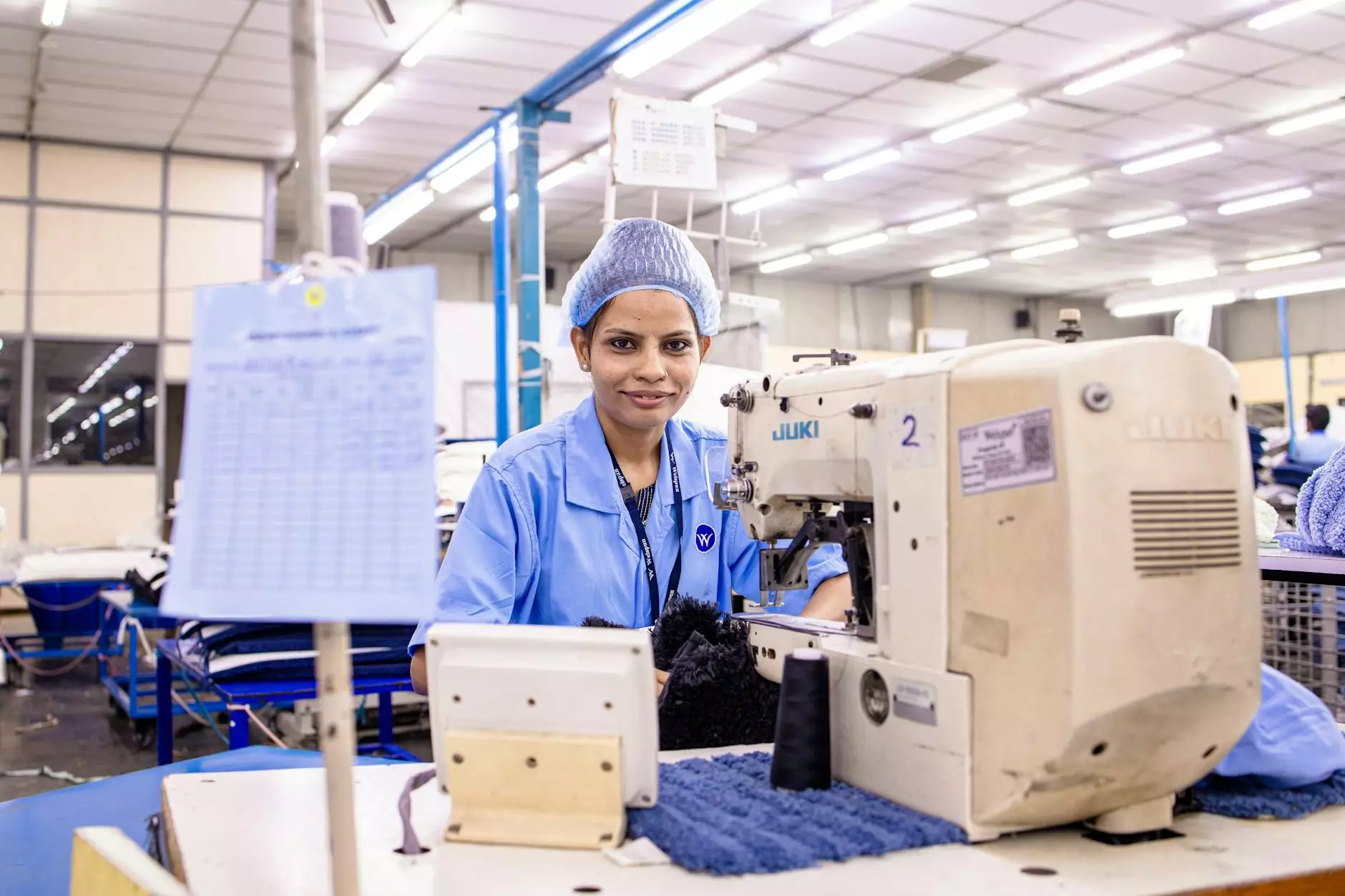
In the dynamic world of manufacturing, CNC machining part factories stand at the forefront of innovation. They are pivotal in fabricating metal components with accuracy, efficiency, and cost-effectiveness. This article delves deep into the world of CNC machining, examining its processes, advantages, applications, and the future landscape shaped by these factories.
What is CNC Machining?
CNC, or Computer Numerical Control, is a sophisticated manufacturing process that utilizes computer software to control machine tools. These machines can perform a myriad of tasks such as drilling, milling, turning, and grinding with remarkable precision. CNC machining allows factories to produce complex parts that would be challenging or impossible to create manually.
The Process of CNC Machining
1. Design and Prototyping
The first step in the CNC machining process begins with design and prototyping. Engineers use computer-aided design (CAD) software to create specific 3D models of parts. This digital model serves as the foundation for the machining process.
2. Programming the CNC Machine
Once the design is established, the next step involves programming the CNC machine using computer-aided manufacturing (CAM) software. This program translates the design into a series of precise movement instructions that the machine will follow to manufacture the part.
3. Material Selection
Material selection is critical in CNC machining. The choice of material impacts the part's durability, weight, and overall performance. Common materials include various metals such as aluminum, steel, brass, and titanium, as well as plastics like nylon and polycarbonate.
4. Machining Process
During the machining process, the CNC machine executes the programmed instructions to cut and shape the material. Factors such as spindle speed, feed rate, and cutting tool geometry are meticulously controlled to ensure high accuracy and repeatability.
5. Quality Control
After machining, the finished parts undergo stringent quality control procedures. Measuring tools and gauges verify the dimensions and tolerances of the parts. This quality assurance step is essential to ensure that every piece meets industry standards and customer specifications.
Benefits of CNC Machining Part Factories
The rise of CNC machining part factories has brought numerous benefits to the manufacturing sector. Here are some key advantages:
- High Precision and Accuracy: CNC machines can achieve tolerances of up to 0.001 inches, making them ideal for producing intricate components.
- Reduced Human Error: Automation minimizes the risk of errors associated with manual machining, leading to more consistent production quality.
- Increased Efficiency: CNC machines can operate continuously, significantly boosting output rates compared to traditional methods.
- Flexibility: These factories can easily adjust to new designs or changes in production, accommodating various industry needs.
- Lower Labor Costs: Automation reduces the labor required for production, translating to lower operating costs.
Applications of CNC Machining
CNC machining is an integral part of various industries, including:
- Aerospace: Manufacturing components with stringent weight and safety requirements.
- Automotive: Producing parts for engines, transmissions, and chassis that require high precision.
- Medical: Creating surgical instruments and implants tailored to specific patient needs.
- Electronics: Fabricating housings and components for devices requiring precise fits and finishes.
- Defense: Manufacturing high-precision parts used in military equipment and systems.
Innovations in CNC Machining
The landscape of CNC machining is constantly evolving, with innovations reshaping the way factories operate. Some noteworthy advancements include:
1. Advanced Software
New CNC programming software enhances the design-to-production workflow, allowing for quicker iterations and more complex geometries without compromising accuracy.
2. Additive Manufacturing Integration
The integration of additive manufacturing techniques such as 3D printing allows for creating hybrid parts that benefit from both subtractive and additive processes, improving material efficiency and functionality.
3. IoT and Smart Factories
The Internet of Things (IoT) is bringing smart technology to CNC machining. Factories can monitor machines in real-time for performance metrics, maintenance needs, and overall equipment effectiveness, optimizing production processes.
4. Automation and Robotics
The use of robots alongside CNC machines for loading and unloading materials increases efficiency while reducing the risk of workplace injuries. This automation leads to safer and more productive environments.
Choosing the Right CNC Machining Part Factory
For businesses looking to partner with a CNC machining part factory, several critical factors should be considered:
- Capabilities: Ensure the factory can handle the specific materials and processes required for your parts.
- Experience: A factory with a proven track record in your industry is more likely to meet your quality and delivery expectations.
- Quality Certifications: Look for ISO and other relevant certifications that demonstrate a commitment to quality management.
- Customer Service: Choose a factory that values communication and works collaboratively to achieve your objectives.
- Cost Efficiency: While price should not be the sole factor, ensure that the factory offers competitive pricing without sacrificing quality.
The Future of CNC Machining Part Factories
As we move forward, the CNC machining landscape will continue to be shaped by technological advancements and changing market demands. With the ongoing integration of AI, machine learning, and enhanced robotics, CNC machining part factories are poised to become even more efficient and capable of meeting the evolving needs of industries worldwide.
In conclusion, CNC machining part factories represent a pivotal sector in modern manufacturing. Their ability to produce high-quality parts with unmatched precision and speed plays a crucial role in the functionality of countless industries. As innovations continue to flow into this field, businesses that leverage these capabilities will find themselves at a significant competitive advantage.
For more information, visit DeepMould.net.